Operations Manager
Job
Overview
- Automotive, Industrial, Manufacturing, Craft
- Engineering and Project Management, Management and Sales
- Permanent
You are subscribed to our push notifications, but not currently for jobs like this.
Would you like to receive notifications for jobs like this as well?
Great news! You are subscribed to receive alerts for jobs similar to this one.
This vacancy has now expired. Please see similar roles below...
Job Summary:
Directly leads a manufacturing team of hourly production personnel and supervision and indirectly leads support team members from production planning, manufacturing engineering, quality and maintenance. This production team is responsible for all aspects of production for all aspects of production for a product line or lines including production planning, staffing, quality improvements, and efficiency improvements and maintaining quality and maintenance requirements.
Leadership and Essential Functions:
• Directs work - Providing direction, delegating, and removing obstacles to get work done.
• Resourcefulness - Securing and deploying resources effectively and efficiently.
• Action oriented - Taking on new opportunities and tough challenges with a sense of urgency, high energy, and enthusiasm.
• Builds effective teams - Building strong-identity teams that apply their diverse skills and perspectives (healthy tension) to achieve common goals. Leverages the benefits of different perspectives
• Communicates effectively - Developing and delivering multi-mode communications that convey a clear understanding of the unique needs of different audiences. Maintain a regular reporting structure for tracking and communicating targets and goals.
• Cultivates innovation - Creating new and better ways for the organization to be successful.
• Health and Safety Fundamentals - Champions and models proactive health and safety behaviors by identifying, reporting and participating in actions to improve health and safety in order to build an interdependent culture and contribute to an injury-free workplace.
• Drives results - Consistently achieving results, even under tough circumstances.
• Leads the development of departmental plans and deliverables. Develop high performance team members to meet / exceed department and organizational goals / objectives.
• Provides technical consultation, leadership, and advice to managers, manufacturing personnel and other functions.
Additional Responsibilities:
• Directs, maintains, and enforces the safety program for the production department you own and reviews safety records to uphold standards of maximum safety for all reports
• Actively participates in safety committee meetings and company initiatives
• Leads production planning activities, with logistics, planning, manufacturing engineering and quality for the assigned area of responsibility
• Provides direction and guidance to others in a way that leads to optimal team performance and meets Key Performance Indicators (KPI’s) such as safety, quality, production and cost
• Selects and collects relevant information, organizes and connects information to task and goals and makes effective decisions
• Independently monitors the progress of daily activities, reports progress, anticipates potential disruptions and develops solutions
• Leads adjustments to activities, tasks and behaviors when changes are necessary to meet customer requirements and company objectives
• Develops and implements new ideas or combination with existing work methods and lean manufacturing practices (Problem identification and problem solving techniques, value stream mapping, use of Kanban/Heijunka systems TPM processes, etc)
• Leads daily production meetings and lead monthly operations review and forecast meetings for the respective area of responsibility
• Creates and implements development plans for assigned personnel to improve overall team performance
• Coaches or mentors direct reports and other team members to develop their skills in problem solving, lean concepts and leadership
• Manages the training process for all associates and ensure training is carried out within assigned area of responsibility
• Facilitates an environment where direct reports make suggestions to improve the production process and results
• Leads and/or participates in Kaizen events, listening to employee suggestions, and promote two-way open communications among all team members
• Actively participates and supports the quality management system including compliance with TS16949, ISO14001, VDA 63 standards; product, process and other audits in assigned area of responsibility
Education:
• Bachelor’s degree from an accredited institution in a technical discipline preferred or combination of equivalent education and experience
Experience:
• 5 to 7 years of experience in a manufacturing environment requirement with 3-5 years of experience in a leadership role in production, manufacturing engineering or technical maintenance support
• Familiar with automotive supplier requirements highly desirable
• SAP enterprise system highly desirable
Specific Skills:
• Possess a solid working knowledge of other business functions such as Logistics, Finance, Engineering, and Human Resources in addition to Manufacturing and Quality
• Strong leadership and data driven decision making ability
• Possess a continuous process improvement mindset with the ability to effectively lead and manage change
• Ability to accurately convey concepts and ideas both written and oral with all levels of the organization
• Able to read/understand component, tooling and machine drawings for troubleshooting
• Ability to collect, organize and analyze data Ability to use data to make effective decisions
• Ability to excel in a team environment and lead cross-functional teams
• Knowledge of manufacturing processes and quality management system processes including PPAP, APQP, PFMEA’s
• Applied use of problem solving techniques and tools (ie A3, Six Sigma, Shainin, etc)
• Applied knowledge and experience in Lean techniques Ability to lead and/or facilitate Kaizen events
• Knowledge of IATF 16949, VDA 63, and/or ISO14001 requirements for applicable manufacturing topics
• Knowledge of Microsoft Office including Outlook, Word, Excel, PowerPoint Familiarity with drawing software such as Visio preferred
• Knowledge of Statistical Process Control
• Ability to travel as needed; expected to be less than 10%
• Ability to work differing shifts to meet business and customer requirements
We are an equal opportunity employer. All qualified individuals will receive consideration for employment without regard to race; color; age; sex; sexual orientation; gender identity; religion; national origin; disability; veteran status; genetic information; or any other criteria protected by governing law.
Sign-up for Job Alerts
Our latest jobs
$ 19 Hourly
United States, Harrison, Ohio
$ 32 Per Hour
United States, Harrison, Ohio
$ 25 - $ 35
United States, Ridgeville, South Carolina
Negotiable
United States, Ridgeville, South Carolina
Negotiable
United States, Ridgeville, South Carolina
$ 19 Per Hour
United States, Harrison , Ohio
Our insights
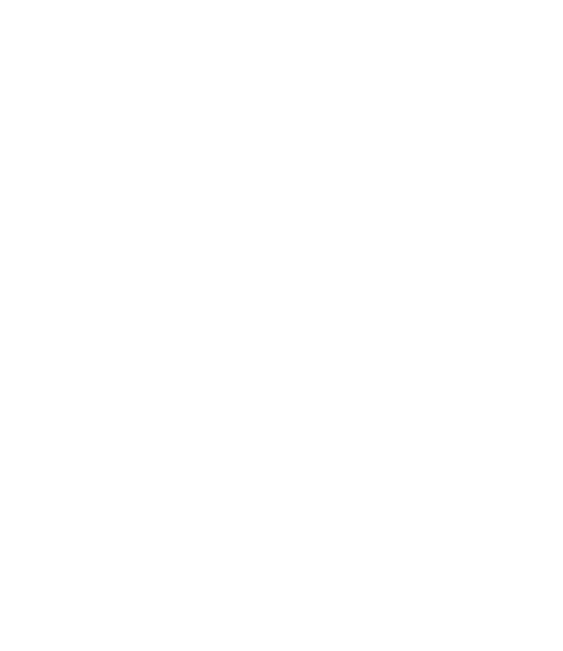
Looking for a new role?